FMT PI Series
PILOT SCALE FERMENTOR : FMT PI Series
- Fermentec's medium-scale and small-scale pilot fermentors are good for producing high-value precision fermentation goods or research. Pilot fermentors that are designed and produced to ASME standards to satisfy international standards cause no corrosion or abrasion, minimize material quality degeneration through delicate processing processes, and are produced after being approved as pressure vessels that are safe in high-temperature and high-pressure situations.
The compact pilot fermentors can be installed in narrow spaces of research rooms, and can be easily operated and maintained and repaired due to their automated systems and proper arrangement of devices. They have adopted the highest-standard controllers to secure precise control and reliability of operation data, and their control program of the highest technology in the industry guarantees improved results. Fermentec's spirit of putting customers' safety first is reflected in the control system and the multiple safety
systems adopted for their vessel part.
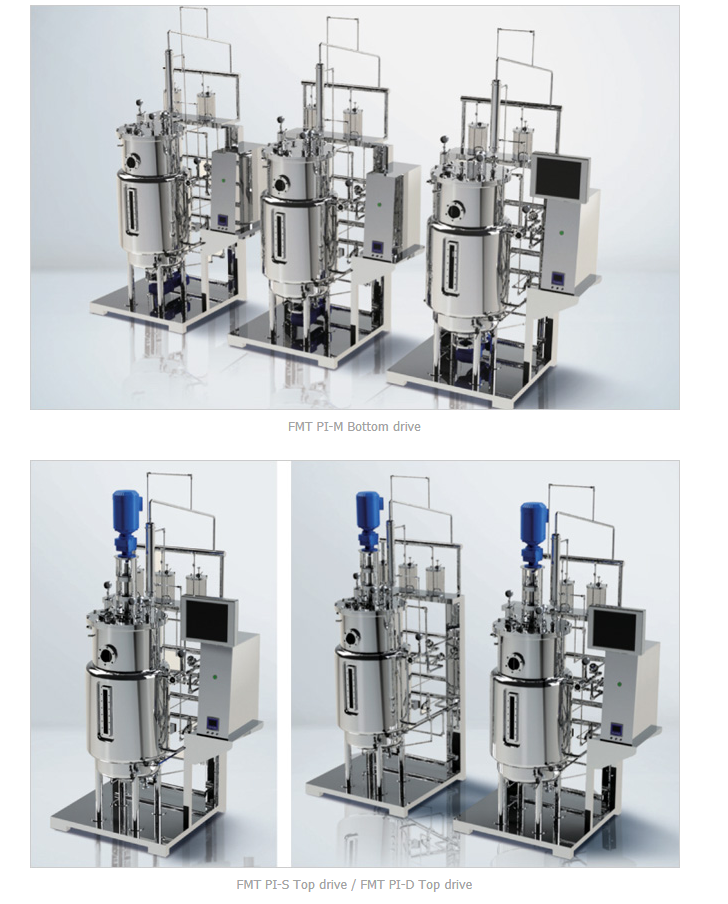
1. Features
· A touch screen computer with HMI that can be conveniently operated
· PLC adopted as a main control system
· Loaded with an interlocking control program to enable the cultivation of various conditions
DO interlocking function - Agitation Speed
FEED interlocking function - dissolved oxygen, supply time
PH interlocking function - feed rate, dissolved oxygen
· A controller with guaranteed reliability has been adopted
· STS316L Vessel + STS304 Jacket (first-class pressure vessel)
· An agitation system: mechanical seal or magnetic drive was used
· Various nozzles made with precisely processed STS 316L and parts guarantee the highest level of confidence
· Elegant design for easy repair and cleaning
2. VesselType
3. Specifications
· High performance design
· Vessel with water jacketed and insulation (STS316L vessel + STS304 jacket)
· Automatic sterilization
· 15~1,000L total volume
· Top plate
-Inoculum port : Flaming (option: Sepum nozzle or aseptic inoculation valve)
-Pressure gauge
-Foam sensor port
-Exhaust port & condenser
-Agitation (top drive only)
-Spare ports
· Upper side wall
-3 media port
-Gas overlay port and spare port
-Transmitter port
-Light
· Lower side wall
-Sparger port
-Sampling port
-Temperature, pH, DO sensor port and spare port
· Bottom
-Harvest
-Agitation (bottom drive only)
· Agitation
-Single or double mechanical seal
-3 baffles or more
· Aeration
-Ring sparger (option : 1~10㎛ micro sparger)
-0.2㎛ disposable hydrophobic filter with check valve
· Impeller
-Rushton type/Pitched blade/Marine blade
· Gas flow
-MFC + bypass rotameter
-Flow rate : max 1 vvm or more
-2 or more MFC (option)
4. Control
· 17" touch screen computer
· 1 to 255 vessels intelligent control
· 16 control loop per vessel
· Temperature control : PID control with water jacket heat exchanger(or heater) and circulation loop
· pH control : acid/base agent
· Agitation control : speed control
· DO control : PID cascade control with agitation, feeding and gas flow rate
· Antifoam control : antifoaming agent
· Feed control : fed-batch control by time, DO, pH
· 8 multi trend log data per vessel
· Easily calibrated sensors
· Level control : electrode type Hi/Low level control load cell type weight control(option)
· Optional sensing unit : ORP, OD, 2nd pH, 2nd DO